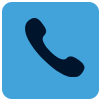
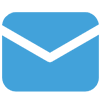
激光选区熔化技术是制备复杂钛结构的重要加工方式,而热处理是必要的后处理手段。首先利用激光选区熔化设备打印TC4合金块体结构,以激光功率、扫描速度及扫描间距为优化对象,以致密度为优化目标开展正交试验,得到成形工艺参数对致密度的影响排序及最优工艺参数。然后对最优工艺参数下的成形样件分别进行消除应力退火处理与完全退火处理,发现消除应力退火前后组织改变较小,而完全退火热处理使微观组织从亚稳态的α′相转变成了α+β相稳定组织,这使拉伸试样在完全退火处理后抗拉强度与屈服强度都有所降低,而延伸率大幅提高。
激光选区熔化(selective laser melting,SLM)技术是一种利用高能激光束对粉末材料进行熔化并逐层打印,进而成形具有复杂结构零件的方法,由于其方便成形复杂结构、集成化程度高,在航空航天、生物医学领域得到了大量的应用。Ti6Al4V合金(简称TC4)是一种具备优异综合力学性能与生物相容性的α+β两相钛合金,由于钛合金本身熔点高、高温下易氧化,传统方法制备困难,因此常采用SLM技术进行加工制造。
通过SLM制备的钛合金零部件的力学性能与成形工艺参数有着密切关系,工艺参数越合理,样件的致密度越高,其力学性能越好。不合理的成形工艺参数会导致零件内部产生孔隙或裂纹,孔隙主要由于气泡和粉末凝固不良导致,而裂纹的形成原因主要是激光熔化后快速冷却产生的残余应力,激光选区熔化材料后的快速冷却会使成形样件内部产生残余应力与不平衡的微观组织,这使得成形零件易产生裂纹、脆性断裂及其他不良影响。因此,优化成形工艺参数与寻找合适的热处理工艺参数是激光选区熔化钛合金课题中的重要工作,目前已有学者对工艺参数优化、力学性能及热处理进行了相关研究。本文将以致密度为目标进行工艺参数优化,结合热处理对显微组织、显微硬度及力学性能的影响进行研究,进而制备出致密度高、力学性能好的钛合金样件。
01 试验部分
1.1 试验材料与设备
试验使用的粉末采用Ti6Al4V商业粉末,其粒径为15~53 μm,具有良好的力学性能、耐腐蚀性、生物性能,其化学成分见表1。打印钛合金所用设备为NCL-M2120打印机,其激光器功率为500 W,光斑直径为40 μm,成形空间尺寸为120 mm×120 mm×100 mm,保护气体为氩气。退火热处理采用SLZK1200-120型3D打印真空热处理炉,具有良好的真空度效果,避免了热处理样件在高温下发生氧化。硬度测量采用HXS-1000AK 硬度测量仪。
表1 TiAl4V合金粉末化学成分
1.2 试验方法
本文采用正交试验法,在不同激光功率P、扫描速度V及扫描间距h下制备尺寸10 mm×10 mm×5 mm的块体样件,设计的正交试验参数见表2,以致密度为考察目标求解最佳参数。使用电火花线切割机床将样件从基板上切割下来并清洗干净,利用阿基米德原理测量块体的致密度,然后对样件进行打磨与抛光处理,使用Olympus光学显微镜观察成形样件截面的缺陷。利用优化工艺参数打印拉伸样件及实心块体,使用真空热处理炉分别进行620 ℃保温2 h与860 ℃保温2 h后炉冷的完全退火处理,退后完成后对拉伸试样进行室温拉伸试验,另外对实心块体进行打磨、抛光和腐蚀,腐蚀试剂配比为H2O∶HF∶HNO3=50∶1∶2(体积比),观察不同后处理下的金相组织并测量显微硬度。硬度测量时施加载荷值为2 N,加载作用时间为10 s,每个面上取10个点进行测量。
表2 正交试验因素水平表
02 结果与讨论
2.1 工艺参数对致密度的影响
2.1.1 正交试验
在试验过程中,多种因素影响打印质量,全面试验势必增加不必要的工作量,采用正交试验可有效缩短试验周期、减少工作量。表3是以激光功率、扫描速度与扫描间距为影响因素,以致密度为评价指标得到16组不同工艺参数下的正交试验结果,可见三种因素都对试验结果有所影响。
表3 正交试验方案及结果
2.1.2 极差分析
采用极差分析能够反映因素水平变化引起的试验结果间的差异,极差R越大,说明该因素的影响越显著。表4是按照极差分析法,得到的正交试验SLM打印件致密度的极差及水平效应比较,可见影响致密度大小的因素排序依次是激光功率、扫描速度及扫描间距,优化的最佳工艺参数为激光功率130 W、扫描速度1000 mm/s、扫描间距0.08 mm。
表4 正交试验打印件致密度极差分析
2.1.3 打印质量评价
图1是SLM正交试验打印的块体样品,总体而言成形质量效果较好,这说明正交试验设计的参数选择较为合理。使用电火花线切割机床将打印块体从钛合金基板上切割下来,然后从致密度和成形截面缺陷两个方面来评价打印质量。
图1 正交试验与最优拉伸试样
理论上需从横、纵两个截面来观察打印块体内部的孔隙情况,但实际研究中纵截面的成形缺陷往往大于横截面上的缺陷,即纵截面的缺陷更加明显,所以此处通过纵截面图来观察不同工艺参数下的成形质量,观察不同程度水平的孔隙缺陷见图2。
图2 不同工艺参数下的孔隙缺陷情况
通过观察打印块体的纵截面,发现孔隙情况比较全面,既有孔隙很多的情况,也有缺陷极少、打印效果良好的情况,这说明最初设定的工艺参数范围较为合理。通过对不同工艺参数下打印块体的孔隙情况分析可知,当小激光功率配合大扫描速度时,打印样件的孔隙缺陷会非常严重,表现为面积较大的块缺陷,进而导致致密度较低。这是由于在小激光功率与大扫描速度时,当前层的钛合金粉末难以充分熔化,粉末粘结效果差,未粘结好的粉末在刮刀下次送粉时的推力作用下与主体发生脱离导致。
2.2 退火工艺对显微结构的影响
2.2.1 显微组织
采用锻造方法制备的TC4样件的微观组织与SLM成形打印具有明显差别,前者主要是粗大的片状晶以及等轴状的α+β相混合组织;而后者在制造过程中由于激光熔化时间短、熔池迅速冷却,导致制造出的样件组织主要是针状马氏体α′相及极少量的β相。
图3是采用不同后处理工艺下的样件显微组织。可见,完全退火后的样件组织由α相和β相组成,这表明亚稳态的α′相在完全退火过程中转化成了α+β相;消除应力退火后的组织与沉积态组织相似,主要是由交错的针状组织组成并伴有少量的颗粒状β相,这表明620 ℃的温度对TC4微观组织相分解提供的驱动力较小,仅能消除成形过程中的残余应力,而860 ℃的高温则为微观组织相分解提供了较大的驱动力。
2.2.2 显微硬度
钛合金的显微硬度差异主要取决于两方面,分别是该钛合金的材料成分差异与内部微观组织的差异,对TC4钛合金的显微硬度差异主要来自微观组织的不同。对于本文显微组织中涉及到的几种成分相,其硬度从大到小的顺序依次为:针状马氏体α′相>α相>β相。
表5是SLM成形TC4钛合金试样在不同退火工艺下的显微硬度,其中FC表示随炉冷却,试验力为0.2 kgf,保持时间为10 s。由图可见,经过620 ℃/2 h/FC的消除应力退火处理后,试样的显微硬度都有所增加,这是由于退火温度较低,相分解的驱动力小,只有少量的针状马氏体α′相发生分解,分解后会产生一些颗粒状的β相并伴随着一定的弥散强化现象,弥散强化作用大于α′相的分解;而经过860 ℃/2 h/FC的完全退火处理后,试样的显微硬度都有所降低,这是由于组织中的α′相大面积分解成α+β相,退火前的α′相为高硬度的过饱和固溶体,在完全退火后的显微硬度要低于未退火的显微硬度。另一方面,晶格结构上的差异也会带来力学表现上的不同,α相作为一种密排六方结构,具有1个滑移面和3个滑移方向,而β相作为一种体心立方结构,具有6个滑移面和2个滑移方向,相对而言β相的塑性变形能力更强,β相含量多的显微组织相应的硬度会低一些。
表5 不同后处理工艺下TC4合金试样的显微硬度
同时由表5还可看出,在三种不同后处理下,纵截面的显微硬度始终高于横截面的显微硬度,这表明激光选区熔化成形TC4显微硬度的各向异性始终存在,纵截面上的各向异性要大于横截面,分析原因包括:① 纵截面上组织主要由针状马氏体组成,横截面上主要是块状马氏体,针状马氏体的组织硬度要大于块状马氏体;② 块状马氏体组织的分解过程要比针状马氏体更简单,相比于块状马氏体直接向网篮组织转变,针状马氏体在转化过程中间还多一步向魏氏体组织转变。相比较而言,纵截面的显微硬度会高一些。
2.3 退火工艺对拉伸样件力学性能的影响
表6列出了沉积态和两组退火工艺下TC4钛合金的力学性能参数。经过620 ℃/2 h/FC退火处理后,试样的抗拉强度提高了61.2 MPa,屈服强度提高了31.3 MPa,而延伸率下降了10.8%。这是由于试样在620 ℃的退火温度下,相分解的驱动力较小,只有少量的针状马氏体发生了分解,分解后伴随产生的一些颗粒状β相出现了一定的弥散强化。
表6 不同后处理工艺下TC4合金试样的力学性能
当试样在860 ℃下进行退火后,抗拉强度与沉积态相比降低127.9 MPa,屈服强度降低117.2 MPa,延伸率提高77.1%。这是由于860 ℃的高温给马氏体分解提供了较大的驱动力,组织中的马氏体α′相完全转变成为α相和β相。马氏体α′相属于过饱和固溶体,强度要高于α相和β相,而在860 ℃退火后,组织中的马氏体含量急剧下降,另外β相聚集长大而失去弥散强化效果,所以在完全退火后试样的强度会降低;同时,不同相的晶格结构会有差异,β相晶格为一种体心立方结构具有12个滑移系,而α′相晶格作为一种密排六方结构仅有3个滑移系,这使β相多的样件具有更好的滑移与延伸特性,因此在完全退火后试样的延伸率会提高。总体而言,完全退火热处理会在损失部分强度的同时较好地提升样件的延展性。
03 结 论
本文通过正交试验法优化激光选区熔化成形Ti6Al4V样件的工艺参数,并研究了两组退火工艺对成形样件显微组织与拉伸力学性能的影响,得到以下结论:
(1)以致密度为目标得到了最佳成形工艺参数:激光功率130 W、扫描速度1000 mm/s、扫描间距0.08 mm, 三个成形参数对致密度的影响大小排序为:激光功率>扫描速度>扫描间距。
(2)两组退火工艺对显微组织的改变差异较大。去应力退火的组织与沉积态组织相似,主要是由交错的针状组织组成并伴有少量的颗粒状β相;完全退火后的组织由α相和β相组成,亚稳态的α’相在完全退火过程中转化成了α+β相。
(3)消除应力退火后由于组织内产生的颗粒状β相带来的弥散强化使得其显微硬度高于沉积态,而完全退火后由于组织的转变其显微硬度低于沉积态。
(4)消除应力退火后的样件拉伸强度相比于沉积态略有提高,这主要是消除应力退火产生β颗粒带来的弥散强化,而完全退火的拉伸样件强度低于沉积态,但完全退火的样件塑性提高了77.1%。
作 者:朱 磊,田宗军,吕 非,梁绘昕
来 源:《电加工与模具》2021年第2期
原 文:《激光选区熔化TC4合金工艺优化及退火处理对显微组织的影响研究》