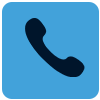
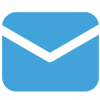
2020 官网升级中!现在您访问官网的浏览器设备分辨率宽度低于1280px请使用高分辨率宽度访问。
In the dynamic landscape of the dental industry, where the shift from labor-intensive to technology-intensive practices is evident, automation technologies are becoming increasingly essential. The integration of 3D printers has already proven successful in the production of dental pieces, particularly in the creation of partial dentures.
After the 3D printing stage, achieving a high-quality finish is paramount. The choice between plasma polishing and traditional hand polishing presents a crucial decision for industries seeking optimal results. Let’s explore the nuanced differences between these methods across four key dimensions: effectiveness, time efficiency, labor cost, and environmental impact.
Effectiveness:
Plasma Polishing:
Employing cutting-edge nano-level technology, plasma polishing achieves unparalleled consistency and brilliance in surface finishing. Its precision extends even to the most intricate geometries, ensuring flawlessly reflective surfaces with minimal imperfections.
Traditional Hand Polish:
While traditional hand polishing can yield satisfactory results, its effectiveness is often compromised by human factors. Despite skilled craftsmanship, maintaining uniformity and eliminating imperfections, particularly in complex areas, poses challenges.
Time Efficiency:
Plasma Polishing:
With an impressive material removal rate of 1μm/min and fully automated processes, plasma polishing significantly accelerates production timelines. What once demanded hours of labor can now be accomplished in a fraction of the time, optimizing efficiency and throughput.
Traditional Hand Polish:
Conversely, traditional hand polishing relies heavily on manual labor and meticulous attention to detail. Each step of the process, from initial abrasion to final buffing, consumes valuable time and resources, inevitably extending production schedules.
Labor Cost:
Plasma Polishing:
By minimizing the need for manual intervention and streamlining operations through automation, plasma polishing offers considerable savings in labor costs. With fewer personnel required to oversee multiple machines, resource allocation becomes more efficient.
Traditional Hand Polish:
The labor-intensive nature of hand polishing necessitates a skilled workforce, often comprising multiple artisans. As each surface is meticulously crafted by hand, labor costs escalate, contributing to overall production expenses.
Environmental Impact:
Plasma Polishing:
In alignment with contemporary environmental standards, plasma polishing utilizes neutral polishing materials that pose minimal risk to ecosystems. Furthermore, its automated processes and efficient material usage contribute to reduced waste generation and resource conservation.
Traditional Hand Polish:
Unfortunately, traditional hand polishing often relies on abrasive chemicals that pose environmental hazards during production and disposal. The handling and management of these substances require stringent safety protocols and incur additional costs for waste treatment.
As industries navigate the evolving landscape of metal finishing, embracing innovative technologies like plasma polishing becomes instrumental in achieving optimal results while minimizing environmental impact. Recognizing this need, Chamlion has introduced the AP10 plasma polishing machine, specifically designed for dental laboratories, with a primary focus on polishing partial dentures.