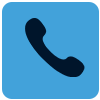
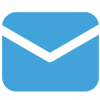
Clara Remacha, Projektleiterin für strategische Accounts für HP 3D-Druck und digitale Fertigung mit Sitz in Barcelona, ist Industrieingenieurin und arbeitet mit Krankenhäusern und Ärzten zusammen, um anatomische 3D-Modelle und eine Vielzahl von Orthesen zu drucken. Sie war Teil des Teams, das den ersten 3D-Drucker von HP auf den Markt brachte und hat in den letzten vier Jahren mehreren Kunden geholfen, 3D-gedruckte Designs in Produktanwendungen umzuwandeln.
Bei einer Networking-Veranstaltung in einem lokalen Krankenhaus im März 2020 warnte eine Ärztin von Remacha sie vor dem Anstieg von COVID-19. Mehr als 1.200 Fälle wurden seit dem ersten Fall am 31.Januar bestätigt – kaum mehr als einen Monat zuvor. Der Arzt schlug vor, dass jeder von zu Hause aus arbeiten und fernfahren sollte. Sicher genug, Spanien hat schon in der nächsten Woche einen Lockdown erlassen.
Was als nächstes in Spanien geschah, wurde ein wiederkehrendes Thema auf der ganzen Welt. Lieferketten wurden gestört, was zu einem Mangel an Waren für Verbraucher und Rohstoffen für die Industrie führte. Krankenhäuser wurden mit COVID-19-Fällen überflutet, und Ärzte waren gezwungen, aufgrund der begrenzten Versorgung auszuwählen, welche Patienten ein Beatmungsgerät bekommen würden. Beschäftigte im Gesundheitswesen und die breite Öffentlichkeit suchten nach persönlicher Schutzausrüstung. Es war ein Albtraum.
Remacha und ihr Team erhielten bald Anfragen von lokalen Krankenhäusern nach 3D-Druckgeräten. Juan Angel Muñoz López, Pflegeaufseher am Krankenhaus Príncipe de Asturias in Alcalá de Henares außerhalb von Madrid, wandte sich an Barcelonas Exzellenzzentrum für 3D-Druck und digitale Fertigung. “Er sagte uns, dass sie bereits an dem Punkt angelangt sind, an dem sie entscheiden müssten, wer lebt und wer nicht. Sie hätten nicht genug Atemschutzmasken für alle”, sagte Remacha. Muñoz wollte die Hilfe von HP bei der Herstellung eines Teils, das das Pflegepersonal der Intensivstation entworfen hatte, das mehrere Standardelemente verbinden konnte, um ein kontinuierliches positives Atemwegsdruckgerät (CPAP) zu schaffen. Das CPAP-Gerät könnte dazu beitragen, den Blutsauerstoffgehalt eines Patienten über 90 Prozent zu erhöhen und sie möglicherweise von der Verwendung eines Beatmungsgeräts zu ersparen.
Innerhalb von zwei Tagen ließen Remacha und das HP-Team das Design bewerten, drucken und zur Validierung ins Krankenhaus zurückschicken. Innerhalb von nur zwei Wochen wurde das CPAP-Querverbindergerät von der Agencia Española de Medicamentos y Productos Sanitarios, der spanischen Medizinprodukteregulierung, zugelassen.
Geschichten wie diese werfen ein Rampenlicht auf die additive Fertigung und ihr Potenzial für eine schnelle, flexible Produktion kritisch benötigter Teile. Ob Gesichtsschutz, Nasopharyngealstupfer oder Atemmasken – die additive Fertigung stellte sich der Herausforderung, die Lücke zu schließen, die durch eine gestörte Lieferkette verursacht wurde. Nun fragen sich einige Branchenbeobachter, ob 3D-Druck die Zukunft der Fertigung sein könnte.
Additive Fertigung steht im Mittelpunkt
Unterbrochene Lieferketten veranlassten mehrere Krankenhäuser, additive Fertigungsunternehmen um Hilfe bei der Herstellung potenziell lebensrettender Geräte zu bitten. Für Unternehmen wie HP war es eine Herausforderung, wie man anfangen sollte.
“Wir hatten keine Ahnung, was nötig war”, sagte Remacha. “Wir entwerfen 3D-Drucker, keine medizinischen Geräte.”
Der erste Schritt von HP bestand darin, ein Online-Formular einzurichten, über das Kunden und Benutzer Anfragen für 3D-gedrucktes Zubehör einreichen konnten, um ihnen zu helfen, COVID-19 in ihrer Community zu bekämpfen. Zunächst wurde nach freihändigen Türöffnern und Maskenverstellern gefragt. Während der Pandemie begannen Gesundheitsarbeiter, nach Gesichtsschutz zu fragen. Remacha und ihr Team hatten ein virtuelles Treffen mit einem der Ärzte, mit denen sie zusammenarbeiten, um das Design für den richtigen Aufbau eines Gesichtsschutzes zu formalisieren.
Das Exzellenzzentrum für 3D-Druck und digitale Fertigung von HP arbeitete eng mit lokalen Krankenhäusern zusammen, um personalisierte PSA zu entwerfen und herzustellen. Fotos: HP
“Wir wussten nicht, welche Anforderungen wir erfüllen mussten. Die Gesundheitsarbeiter arbeiteten jetzt 12-Stunden-Schichten und sie sagten uns, dass Komfort einer der wichtigsten Faktoren sei”, sagte Remacha.
Das HP Team traf sich an einem Samstag und hatte bis Montag einen Gesichtsschutz-Prototyp mit verstellbarem Band entworfen und gedruckt. Das Team benutzte Taxis, um Teile zwischen dem Krankenhaus hin und her zu transportieren, um Passform und Funktionalität zu gewährleisten. Am darauffolgenden Freitag war das Design in seiner vierten Iteration. Einige Wochen später erhielt das Design die vollständige Zertifizierung nach dem europäischen EN-166 Standard.
Empfohlen für Sie: Lakshmi Vendra Bewertungen AM’s Einsatz in Öl und Gas
Seit der Ankündigung ihrer Bemühungen, der medizinischen Gemeinschaft zu helfen, produzierten HP und seine globalen Community-Partner mehr als sechs Millionen Teile für medizinische Anwendungen.
Die Leichtigkeit der Vorschriften und Standards hat der additiven Fertigung während der Pandemie maßgeblich geholfen. In den USA erteilte die Food and Drug Administration (EUA) eine Notfallzulassung für den 3D-Druck von Teilen für medizinische Anwendungen. So erhielt Formlabs aus Somerville, Maß, eine EUA, um BiPAP-Adapter (BiPAP) in Krankenhäusern in den USA zu drucken und zu versenden, um Beatmungsmangel zu Beginn der Pandemie zu bekämpfen.
America Makes ist einer der führenden und kollaborativen Partner des Landes in Forschung und Innovation in der additiven Fertigung und 3D-Drucktechnologie. Zu Beginn der Pandemie dokumentierte America Makes gemeinsam mit ihrem Partnernetzwerk eine Reihe von Themen rund um die Lieferkette und stellte diese dem Kommissar der FDA vor.
“Innerhalb weniger Tage nach Beginn der Pandemie haben wir der FDA gesagt, dass die AM-Community bereit ist, zu helfen. Sie sitzen am Rande und können sich nicht engagieren, weil sie keine Antworten auf diese verschiedenen [regulatorischen] Fragen kennen”, sagte John Wilczynski, Executive Director bei America Makes. “Fast sofort begann die Zusammenarbeit zwischen der Veterans Health Administration (VA), der FDA und dem National Institute of Health (NIH) zwischen der Veterans Health Administration (VA) und der FDA. Es gab einen enormen Informationsfluss, der an die AM-Community weitergegeben wurde, was den Herstellern beim Start half.”
On-Demand-Fertigung heute
Die Pandemie hat Krankenhäuser ermutigt, eine On-Premise- oder On-Demand-Fertigung in Betracht zu ziehen. Systeme wie die VA haben erhebliche Fortschritte bei der Herstellung von Point-of-Care-Geräten gemacht, wie z.B. 3D-Druck vor Ort. Laut Wilczynski bietet die Pandemie eine Chance, die Lieferkette und die Herstellung von Teilen zu überdenken.
“In den meisten Fällen sind die Menschen diesen Weg nicht gegangen”, sagte Wilczynski. “Das Beschaffungssystem im Gesundheitswesen bietet nicht die Freiheit, einen einzigen $50-Artikel zu kaufen, der normalerweise $1 für den täglichen Gebrauch kostet, aber mit AM können wir das. Es ist eine interessante Idee, weil wir von einem Verbrauchsmaterial zu einem Mehrweg-Ansatz wechseln.”
3D Systems in Rock Hill, S.C., hat sich mit der VA zusammengetan, um medizinische Geräte zu entwerfen und sie durch die FDA-Zulassung zu führen. Die beiden Organisationen werden AM-Lösungen einsetzen, um medizinische Geräte der nächsten Generation an Point of Care bereitzustellen.
Die Initiative entstand aus der ersten Zusammenarbeit zur Bekämpfung des Mangels an Gesichtsmasken in den VA-Krankenhäusern zu Beginn der Pandemie.
Als nächstes sollte ein 3D-gedruckter Nasopharyngealstupfer (NP) entwickelt werden, der auf Produktionsanlagen hergestellt werden konnte. Der Mangel an NP-Abstrichen war eine erhebliche Hürde, da die groß angelegten Tests zunahmen. 3D Systems konnte ein kundenspezifisches NP-Tupferdesign in medizinischer Qualität aus DuraFrom ProxX PA mit seinem ProX SLS 6100 Drucker testen und validieren. Das Material ist ein starkes, robustes thermoplastisches Material, das für ausgewählte medizinische Geräte wie NP-Tupfer geeignet ist. Das Unternehmen konnte rund um die Uhr 3.000 Tupfer pro Drucker herstellen.
“Was während der Pandemie als Reaktion auf einen kritischen Bedarf begann, hat sich ausgeweitet, um die Art und Weise der Gesundheitsversorgung zu verändern”, sagte Menno Ellis, Executive Vice President of Healthcare Solutions bei 3D Systems. “Dies ist eine einzigartige Zusammenarbeit zwischen einem Anbieter von additiven Fertigungslösungen und einem der weltweit größten integrierten Gesundheitssysteme, um Innovationen in der Produktion und Bereitstellung von Medizinprodukten zu beschleunigen.”
3D Systems hat viel Erfolg bei der Bereitstellung von On-Demand-Anwendungen in der medizinischen additiven Fertigung in der Dentalindustrie. Zahnmedizinische Geräte, einschließlich Kronen, Brücken und Prothesen, werden in hoher Stückzahl und bedarfsgerecht in additiver Fertigung hergestellt. Zum Beispiel würde der Zahnarzt einen intraoralen Scan machen und einen digitalen Eindruck erstellen, der sofort analysiert wird. Wenn ein 3D-Drucker vor Ort ist, könnte der Zahnarzt noch am selben Tag eine Probeform herstellen und am Patienten testen. Der Patient nimmt die Form mit nach Hause, um sie für ein paar Tage zu versuchen, bevor er die Zahnfixierung fertigstellt. Der gesamte Prozess reduziert das, was früher Wochen in Tage dauerte.
“Wir sehen einen zunehmenden Einsatz patientenspezifischer Instrumente und medizinischer Geräte und erwarten, dass sich dies weiter beschleunigen wird”, sagte Ellis. “Hier glänzt der 3D-Druck und hebt sich von anderen Technologien ab, denn man hat den Vorteil, dass man in einer Einheit produziert und die Individualisierung ganz praktisch und für den Menschen zugänglich macht.”
Lesen Sie unseren Fertigungsblog: Integration von AM in den industriellen Betrieb
Im Zuge der anhaltenden Pandemie hat sich die additive Fertigung als praktikable Lösung für zeitsensible Produktion erwiesen. Wenn die Dentalindustrie als Beispiel dienen kann, kann sie zu einer Lösung für die On-Demand-Produktion werden. Was sind also die nächsten Schritte, um ein vollständig verteiltes und Netto-Null-Produktionsnetzwerk zu schaffen?
Distributed and Net Zero Manufacturing
Während die additive Fertigung während der Pandemie viele Erfolge verzeichnet hat, blieb sie nicht ohne Rückschläge. Die Luft- und Raumfahrt- und Automobilindustrie verzeichnete während der Pandemie erhebliche Verluste. Der Mangel an Neugeschäften hat der Branche geschadet: GE musste 10.000 Arbeitsplätze in der Luftfahrt kürzen, Boeing hat die Flugzeugproduktion gekürzt und Airbus berichtet über 55-prozentige Umsatzverluste. Für beide Branchen wird additive Fertigung zur Herstellung von Hardwarekomponenten eingesetzt, insbesondere Metall-3D-gedruckte Teile.
Richard Collins, Principal Analyst bei IDTechEx in Cambridge, England, sprach darüber, wie sich die additive Metallindustrie verschlechtern wird, bevor sie besser wird. IDTechEx veröffentlichte kürzlich den Bericht Metal Additive Manufacturing 2020-2030, der die Trends von 2020 und die Zukunft der additiven Fertigung im nächsten Jahrzehnt zusammenfasst. IDTechEx hob im Bericht hervor, wie die Druckkosten sinken, da neue Pulver- und Rohstoffvarianten auf den Markt kommen. Der allmähliche Rückgang der Materialkosten, die Reife der Lieferkette und der zunehmende Wettbewerb werden einen größeren Markt für additive Fertigung fördern.
Während das Unternehmen berichtet, wie sich COVID-19 negativ auf die additive Fertigung von Metall ausgewirkt hat, wird davon ausgegangen, dass der Effekt kurzfristig sein wird. Die Pandemie hat Unternehmen gezwungen, in die Zukunft der additiven Fertigung zu investieren. Immer mehr Marktteilnehmer werden innovative Verfahren und Materialien entwickeln, um die Herstellung additiver Fertigungsteile zu erleichtern. Zwischen 2017-2019 gab es bemerkenswerte Aktivitäten im Metallpulver für die additive Fertigung; Dies war vor allem in der Luft- und Raumfahrtindustrie von Carpenter, GKN und AP&C, einem GE Additive Unternehmen. In 2020 ist eine große Materialentwicklung geblieben, die im kommenden Jahrzehnt weiter wachsen wird.
“Es gab negative Auswirkungen, aber wir haben begonnen, nach vorne zu schauen und neu zu bewerten, wie die Menschen die verteilte Lieferkette betrachten”, sagte Collins. “Wenn Unternehmen ernsthaft über eine verteilte Lieferkette nachdenken, ist die additive Fertigung ein wichtiger Partner.”
Die Motivation hinter der verteilten 3D-Netto-Null-Fertigung besteht darin, die Herausforderungen globaler sozialer, wirtschaftlicher und ökologischer Trends anzugehen, die während der Pandemie hervorgehoben wurden. Der Erfolg erfordert eine systemische Perspektive und Betrachtung der 3D additiven Fertigung als kyberphysikalische Lösung, die durch die Integration von Betriebstechnologien (OT) und Informationstechnologien (IT) aufgebaut wird. In einer digitalen 3D-Fertigungsumgebung – die 3D-Druckgeräte, Stromversorgungs- und Supportgeräte – sind OT, Datenerfassungsgeräte und Computerausrüstung die IT.
“Es gibt eine Reihe von 3D-Technologien, die von der Kunst zum Teil gehen können”, sagte Chandrakant Patel, Chief Engineer bei HP und ASME Fellow. “Durch den Bau von Mikronetzen der Produktion braucht man keine gigantische Anlage zu bauen. Wenn man modulare Fabriken weltweit verteilt und mit lokalen erneuerbaren Energiequellen wie Solarenergie und sogar Abfallströmen (Methan aus der anaeroben Vergärung von Mist von Milchkühen zum Beispiel) betrieben hat, kann man jetzt in Richtung Netto-Null-Produktion fahren.”
ASME TechCast: Additive Fertigung revolutioniert Luft- und Raumfahrtdesign
In der Dezember-Sonderausgabe der Brücke für die Nationale Akademie der Ingenieurwissenschaften schrieb Patel: “In der digitalen 3D-Fertigung besteht der OT aus 3D-Druckern, und die IT-Art-to-Part-Pipeline beginnt mit dem Teiledesign überall auf der Welt. Dann ist es die Übertragung digitaler Daten, um Teile an einem bestimmten Ort zu drucken und an den Kunden zu liefern. Die bedarfsgerechte Bereitstellungskapazität der digitalen 3D-Fertigung [während der Pandemie] hat gezeigt, dass sie belastbare Lieferketten ermöglichen kann.”
Laut Patel erfordert der Erfolg der digitalen 3D-Fertigung eine ganzheitliche Perspektive, die Design, Geräte und die digitale Fabrik umfasst. Wenn es um Design geht, kann der Designer die Fähigkeit des 3D-Drucks nutzen, Formen und Konturen zu erstellen, die zuvor mit der richtigen Wahl der 3D-Drucktechnologie nicht möglich waren. Mit einer Reihe von additiven Fertigungsdruckern, die jetzt verfügbar sind, müssen Designer und Entwickler die Herstellung von Teilen überdenken. Das Modell des Kaufs überschüssiger Teile muss sich auf kleinere Chargen hochgradig kundenspezifischer Teile verlagern. Genau wie die zahnärztlichen Vorrichtungen passen diese Teile genau an die Anforderungen des Projekts an – Präzision und Feinabstimmung durch den Ingenieur.
In Bezug auf die 3D-Druckergeräte und die digitale Fabrik stehen große Mengen maschinell generierter Daten zur Verfügung, um genaue und schnelle Ergebnisse zu liefern.
“In diesem Zusammenhang ist es jedoch falsch, das 3D-Druckergerät als Black Box zu behandeln, wobei davon ausgegangen wird, dass große Datenmengen vom Drucker und KI allein die genauen Ergebnisse liefern”, sagte Patel. “Ein tiefes Domänenverständnis der Physik- und Materialwissenschaften ist grundlegend für ein erfolgreiches Modell des Betriebs der 3D-Art-to-Part-Pipeline an der Schnittstelle von Domäne, Daten und KI.”
Die Welt verändert sich
Es gibt noch Hürden zu überwinden, bevor eine verteilte Fertigung erreicht werden kann, wobei die Vorschriften die höchsten sind. Die Pandemie dauert noch an, aber mehrere Lieferketten sind wieder normal produziert worden. In den ersten Monaten der Pandemie wurden die erzielten Fortschritte durch die von der FDA erteilten EUAs stark angeregt. Laut Wilczynski war der Notfall im Gesundheitswesen ein wichtiger Katalysator für die Branche.
“Sobald die EUAs auslaufen, dürfen nicht mehr auf unkonventionelle Weise hergestellte Komponenten verwendet werden. Es wird davon ausgegangen, dass die derzeitige Reihe von Vorschriften und Anforderungen das Beste für die Branche ist”, sagte Wilczynski.
Doch wie Remacha und ihr Team entdeckten, galten einige der Vorschriften nicht in einer additiven Fertigung.
“Wir kannten die Regulierungskultur in der Medizinbranche nicht. Wir haben die Agentur angerufen, um sicherzustellen, dass sie über alle Informationen verfügt, und es dauerte lange, bis sie die Dokumentation überprüfen konnten”, sagte Remacha. “Am Ende fand die Agentur Bereiche, in denen die Anforderungen [für additive Teile] keinen Sinn machten, und für die folgenden produzierten Teile war es einfacher, sie zu zertifizieren.”
Mit den Änderungen der Vorschriften, der Schaffung neuer Materialien und dem sinkenden Preis für 3D-Drucker wird die additive Fertigung immer mehr machbar.
“Es gibt einen Grenzpunkt für verschiedene Technologien. Je nachdem, wie viele Teile Sie benötigen und welche Anpassungen erforderlich sind, ist 3D kostengünstiger”, sagte Patel. “Aber wenn Sie sagen, dass sich die Welt hin zu einem hoch personalisierten, maßgeschneiderten, individualisierten und bedarfsgerechten verteilten Fertigungsmodell entwickelt, das nachhaltig ist, werden wir sehen, wie sich die Welt in Richtung additiver Fertigung bewegt.”
Carlos M. González ist Sonderprojektleiter.